- Point of view
Your guide to Industry 4.0: How data analytics and cloud technologies are enabling the factory of the future
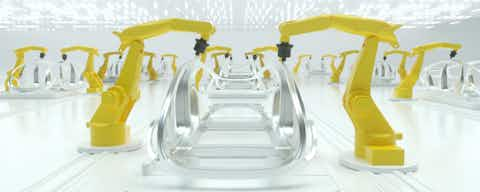
Why it's critical for manufacturers to embrace Industry 4.0 and how you can implement it in your organization.
The new normal is here. And it's not just digitized, it's dynamic – characterized by sharp demand swings, unexpected supply chain challenges, and economic uncertainty. You know you need to improve your organization's ability to adapt at speed. And you understand that smart technologies are now critical to helping your organization thrive in the new normal. But how do you move forward and enable the future of manufacturing?
In this guide, we explain how advanced digital technologies are coalescing to drive the Fourth Industrial Revolution – or Industry 4.0. We explore:
- The underlying trends that are driving Industry 4.0 adoption among manufacturers
- Key opportunities and challenges along the road to Industry 4.0
- Actionable insights from our work helping manufacturers transform their operations to adapt to the new normal
So, what exactly is Industry 4.0?
In simple terms, Industry 4.0 is the harnessing of connectivity, artificial intelligence (AI), flexible automation, and cloud to transform manufacturing. Though AI-powered sensors and other advanced technology enable connectivity and data capture, the cloud serves as a scalable platform where manufacturers can use and store vast amounts of data, apply business intelligence and advanced analytics, and then use those insights to impact their manufacturing operations in real time.
Think of it like this: the First Industrial Revolution was about applying steam and waterpower. The second was about mass production. Both the third and fourth revolutions have been about automation. But while in the Third Industrial Revolution, automation was applied using IT systems and a set of rules humans created, in the fourth revolution, machines take center stage. They talk, learn, and interact with each other. And they provide humans with insights that are driving real business agility, speed, and outcomes.
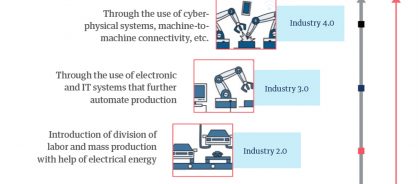
Do we need another revolution?
The short answer is yes. In today's rapidly changing global market, dealing with uncertainty requires manufacturers to become adept at predicting and reacting to shifts in demand, supply chain interruptions, and changing market conditions. Combining multiple Industry 4.0 technologies provides the muscle needed to do this.
But that's not all. The events of the past 18 months have made it clear that manufacturers today must have the agility to pivot to remote work at short notice. And this is only possible with a high level of industry automation that can enable manufacturers to remotely monitor and manage their production lines.
Indeed, by combining technologies like IoT sensors, mobile devices, 5G connectivity, machine learning, and advanced analytics – with cloud as the foundational enabling technology – manufacturers can not only react quickly to changing market dynamics, but they can also start to create a competitive edge in their respective markets.
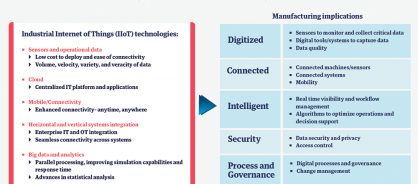
How are Industry 4.0 technologies used?
Manufacturers are capturing value from integrating Industry 4.0 technologies into their operations in a number of ways. Here are four use cases we are seeing more frequently.
- Advanced plant maintenance: By embedding smart sensors into factory assets, manufacturers are monitoring for early warning signs of failures or service requirements. Predefined trigger points prompt automatic actions such as part replacement, rerouting work, or – if necessary – line shutdowns.
- Improved supply chain visibility: Many manufacturers are now putting smart sensors into packaging, shipping vehicles, and inventory storage systems to get a real-time, accurate view of inventory as it ships and is consumed. That's providing greater agility to deal with unpredicted disruptions.
- Real-time production view: Using machine-to-machine connectivity, some manufacturers are getting a fresh view into their production lines and key manufacturing process stages. With better communication between nodes, the flow of goods can streamline for just-in-time delivery.
- Identifying noncompliance: Sensors and other AI technologies provide quality control checkpoints right across the production line. By spotting specification noncompliance early, these manufacturers are avoiding unnecessary waste and downtime.
The benefits of Industry 4.0
Depending on your business niche, operating model, and business objectives, the value of Industry 4.0 could be seen in many ways.
Our work helping manufacturers adopt Industry 4.0 technologies and strategies suggests the benefits could include:
- Data-driven decisions enabled by the move to cloud
- Shop managers freed up to spend more time in optimizing operations
- Improved productivity
- Faster time to market
- Greater agility and flexibility
- Better employee and customer experiences
- Reduced costs
- Enhanced regulatory compliance
- Improved operational visibility
- Improved innovation opportunities
- Greater revenues and profitability
Simply put, Industry 4.0 enables manufacturers to become more digitized, smarter, connected, and agile. And the data speaks for itself. In a study by the Business Development Bank of Canada 60% of adopters of digital technologies said that digitization improved their productivity. The same study also found that 50% of digital technology adopters said that it helped them cut operating costs while 42% reported a boost in overall quality.
The challenges of implementing Industry 4.0
Let's be clear, there are no out-of-the-box solutions for adopting Industry 4.0 technologies and strategies. To really capture the value of Industry 4.0, you need to bring together more than just diverse technologies. You also need deep functional knowledge, process reimagination, technology expertise, and operational change management skills. And that makes the journey more challenging – but also more impactful.
Our work with leading manufacturers suggests there are four areas where manufacturers commonly struggle on their journey toward Industry 4.0 enablement.
- Creating operational visibility: Setting up a central control system that can monitor and control end-to-end operations and systematically track machine health, availability, quality, and throughput
- Streamlining product scheduling and control: Achieving real-time visibility into order and job status to track schedule variances and integrating and automating systems to provide greater operational control
- Leveraging advanced analytics: Rapidly improving data management and analytics capabilities to enable the predictive and prescriptive optimization of assets and resources using massive volumes of data
- Acquiring skills and capabilities: Finding resources with the right experience to successfully help your organization rearchitect your on-premise systems, reimagine your existing process, and make the most of data on cloud
What does success look like?
We recently worked with a global plastics manufacturer to adopt Industry 4.0 technologies and strategies. Today, Industry 4.0 technologies are helping the organization shave $2 million off in operating costs per year. And incorrect raw materials have decreased by more than 80%. That equals big savings and greater agility. Plus, the manufacturer now has unprecedented insight into their data by migrating data and analytics to the cloud to improve their real-time production visibility and enhance their operational effectiveness. And that means they will be better prepared to handle unexpected demand swings and supply chain bottlenecks in the future.
How can I enable Industry 4.0 in my organization?
Like any large-scale transformation, much will depend on your organization's current technology, strategy, and capacity for change. Every organization will be different, and every Industry 4.0 journey will vary in pace, direction, and results.
Some common considerations may include:
- Leveraging cloud and moving data to the core of your business operations
- Adopting technology to enable seamless internal and external collaboration
- Harnessing analytics to generate data-driven insights to spot risks and opportunities
- Embedding AI into your operations to augment human intelligence
- Deploying operating models that promote diversity, equity, and inclusion
- Partnering with a trusted advisor who understands your business deeply
Visit our industrial manufacturing page
Let's get started
For manufacturers looking to thrive in the new normal, adopting Industry 4.0 technologies and strategies is not just nice to have – it is an absolute imperative. There's no time to waste. Get out there, learn more about Industry 4.0, and use our guide to consider how to experiment and innovate, and help your organization move into the future of manufacturing with confidence.