- Article
Leveraging the power of cloud in the media content supply chain
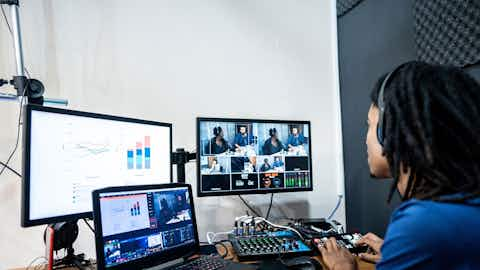
Pre-pandemic, the idea of using cloud services for content production was on a slow burn, with broadcasters preferring a cautious approach to adoption due to security and reliability concerns. These were quickly overcome as the increased need for elasticity (both up and down), scale, performance, collaboration, and evolving consumption patterns have turbocharged cloud adoption across the content supply chain.
Cloud-based virtual production, distribution, and monetization can address both economic and competitive challenges, including higher demand for original and live content, high inflation, and lack of highly skilled resources. Plus, it lays the foundation to use artificial intelligence (AI), machine learning (ML), and data analytics to enhance workflows and improve ROI.
The media and entertainment (M&E) business cycle that was once all facility-based now needs to include cloud services components. This new digital business model means all internal workflow orchestration must also be on-demand. The need for collaboration across a distributed workforce, a global footprint, and distribution to web, mobile, and connected TV (CTV) are all driving cloud services. The challenge is unifying and testing facility-based systems with cloud services to facilitate hybrid environment applications.
Industry challenges and opportunities
As M&E business models adapt to a direct-to-consumer (DTC) world, it's become increasingly necessary to reorient all intermediate workflows so they're orchestrated with customer experience in mind. This has resulted in multiple challenges to revenues and the cost of operations.
- Pay-TV cord-cutting. The pay-TV market continues to shrink. As cord-cutting continues, over-the-top (OTT) distribution will grow, including new OTT services, DTC video services, virtual pay-TV services, and existing OTT offerings. The industry understands the future is based on OTT services rather than legacy pay-TV, and consumers are willing to pay for multiple OTT subscriptions, which will drive market growth, support multiple winners, and keep video spending strong
- Delivering high-speed connectivity. Continued cord-cutting in pay-TV has turned the attention of the industry to broadband internet services to provide consumers high-bandwidth connectivity to support their appetite for OTT video streaming services
- Increased content licensing fees. As spending on streaming content skyrockets in the media and entertainment industry, a new formula is needed to drive a sustainable return on investment. The surge in consumer demand for streaming video content is yielding blockbuster deals as well as a steep increase in the cost of sports rights – estimated to be $29.5 billion in the US alone in 2024, according to Statista. To overcome these high costs for programming, the industry must think differently about everything, from more cost-efficient ways to produce content to improved distribution and monetization processes. This includes migrating to SaaS-based cloud services combined with AI/ML and data analytics to facilitate workflows and create more value to offset higher programming costs.
- Content creation and production cost containment vs. cloud services and content delivery fees. Remote workflow concepts are increasing in popularity as higher demand for original and live content, compressed timelines for content creation and delivery, high inflation, and lack of highly skilled resources have blown up budgets. These software-defined workflows (SDWs) span the media ecosystem, allowing assets, systems, and processes to be joined and run together. They handle repetitive tasks and can optimize pipelines by allowing content to be processed frequently and quickly. The major cloud service providers, including Amazon AWS, Google Cloud, Microsoft Azure, and others, are investing heavily in infrastructure as a service (IaaS), platform as a service (PaaS), and (software as a service) SaaS at all levels to address increased demand while also addressing security, latency, and workflow efficiencies using advanced AI/ML and data analytics to create smarter solutions. But not all vendors provide an end-to-end cloud-based solution that covers all aspects of work, meaning production teams often must move from service to service
- The future of streaming. The future of streaming will not be limited to subscription business models. It will include a scaled approach with tiers for subscription-only, hybrid, and ad-supported models that allow for an increase in the overall total addressable market. It will include revenue coming from subscriptions, advertising, and ecommerce with the introduction of contextual actionable advertising where an immediate transaction can take place on the connected device
Applying AI, ML, and data analytics to the business cycle (cloud production, distribution, and monetization)
According to the International Trade Association for Broadcast & Media Technology (IABM), 32% of the M&E industry had already deployed AI/ML technology by the end of 2022, and most companies with media content business models are planning to deploy AI/ML over the next few years.
The primary drivers of the adoption of AI/ML include the opportunity to automate routine workflows and gain increasing insights into audiences, which are vital for DTC models. On the front end, AI/ML is helping content creators make decisions that maximize ROI, whereas most use cases of AI/ML in content creation and production are to automate production and post-production processes. The same applies to content management, where AI/ML automates routine tasks such as metadata tagging, image recognition, audio/video recognition, and speech to text.
Use cases include:
- Media companies equipping camera systems with more advanced AI/ML edge features to capture more context and intelligence from the content that they are creating
- End users leveraging AI/ML to automate operations to produce higher quality sports and entertainment content with fewer resources as the demand for live content increases
- Syncing and grouping video clips and automating mundane, time-consuming tasks in post-production to save time and avoid bottlenecks
- Automating matching content delivery to destination profiles to improve reliability, quality of service (QoS), and quality of experience (QoE)
- Metadata tagging in content management to improve the level and detail of metadata and the value of content through search, discovery, personalization, and content performance
- Augmenting rights management, content planning/scheduling, subscriptions, and data analytics to support advertising in content monetization
- Predicting viewer behavior and turnover, analyzing renewal history, and providing valuable insights for QoS, QoE, and proactive viewer retention and acquisition strategy, decisioning, and management
- AI script analysis can make decisions on the best content genre for a particular script
From content creation, production, and publishing to distribution and monetization, AI/ML is still in its infancy regarding the complete orchestration of the entire business cycle. The importance of laying the breadcrumbs everywhere along the content and consumer journey and then using them collectively to synchronize and optimize the demand and supply cannot be understated.
A media factory in the cloud
The M&E industry is at an inflection point in the transition to live and on-demand cloud services. The ultimate goal is to have a complete 100% media factory of the future, with lean and real-time characteristics across the value chains that comprise the entire business cycle, including production, distribution, and monetization. Meanwhile, the industry is taking a cautious approach by adopting a hybrid model where some processes remain facility-based while others are transitioned to the cloud. The transition to cloud services allows the industry to rethink its current workflows and innovate by leveraging advancements in AI/ML and data analytics.