- Point of view
Four ways supply chain leaders can build resilient teams and attract talent
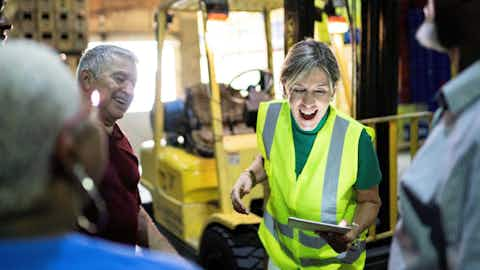
Inflation. Geopolitical turmoil. Recession. Labor challenges. Changing consumer dynamics. Speed of technology innovation. There's never been a more crucial time to reinforce your supply chain operating models and, more importantly, your team’s. Every challenge is a new opportunity. And that's why we gathered a panel of supply chain leaders from across industries to share their thoughts on navigating 2023 and discuss strategies to help organizations empower their existing teams.
We started by asking what's keeping them up at night. To no one's surprise, improving workforce productivity in a tough labor market got unanimous nods. Rick Camacho, chief supply chain officer at SC Johnson, worries: “There's just so much going on right now. I've never seen this amount of work and effort required in the 30+ years I’ve been doing supply chain. And it’s just the urgency, the quantity, that keeps me up at night.”
But there's light at the end of the tunnel. And some neat ways to achieve the right mix of technology and traits to build resilient and agile supply chains while empowering your workforce to engage in more value-added activities to improve retention and attract the next generation of talent.
1. Data-savvy teams find credible answers
There's no denying that. But data adoption is still a challenge that sits at the crossroads of re-tooling individuals with an analytical inclination and resolving the historical problem of pockets of data creating multiple ‘truths’ across an enterprise. To build a data-literate team, you should nurture a mindset that appreciates its impact.
Data analytics is a game changer for improving agility, resilience, scenario planning, and transparency in the supply chain. Though data insights alone will not build a perfect plan to combat volatility, they can empower you to mitigate risk, pre-define resolution plans, and boost forecast accuracy of demand by identifying customers' buying patterns for agile inventory management and responsiveness. Arpad Hevizi, VP of digital value creation at Qualcomm, further elaborates: “The problem’s become a lot more complex because it's not just about doing more or securing more supply. It's about how to optimize and make decisions. And visibility has dropped significantly in the last two years because we created many supply chain layers, not just within the company. How can we fix that? This is where better supply chain analytics, better way to detect is more important.”
2. Automation is part of your survival kit.
In an unpredictable world, speeding up delivery processes becomes non-negotiable. Automating supply chain processes improves a team's flexibility and efficiency while reducing service costs. More importantly, automation improves the quality of life, and the value employees derive from their activities. Why spend time performing repetitive tasks when you can spend your time solving real problems? For example, your source and procurement teams can get automatically alerts about upcoming demand signals to avoid stock shortages.
According to Sara Park, VP of E2E integrated planning at the Coca-Cola Company, automation tools are a great ally: “I'm giving my team lots of flexibility to get their work done and tools and capabilities to help them. And we're also automating a lot of redundant work with RPA. We're giving them opportunities to learn Alteryx, for instance, to be more effective and efficient in a 40-hour week. Many people on the team want to advance and learn something outside of their core jobs. So, we say, OK, match up."
3. Environmental, social, and governance (ESG) focus will keep you relevant.
Today, ESG roadmaps are baked into business-level visions because purpose-driven millennials and Gen Zers gravitate to employers who are working toward a net positive impact. Educating your teams early on about sustainable practices will help them align meaningfully with the right suppliers. And build trust among stakeholders to ensure work productivity and long-term loyalty. Paul Myler, VP of supply chain planning and customer care at Graphic Packaging International, argues: “You better be out there doing the right thing because, you know, people, especially the younger generations, will not work for you if you don't do the right thing."
KC Rakam, head of customer engineering at Google, feels there's a cost benefit as well: “I'm a big fan of sustainable practices. And it's embedded into Google's culture. If you take, like, the data centers, we are carbon neutral and have plans to go completely carbon-free by 2030. It has a cost implication because overall, you're not only making the planet better but also reducing the cost."
4. Stay humble. Stay curious.
Changing the collective mindset of your team is no easy feat. You go through numerous learnings and roadblocks to get each spoke of your supply chain wheel working frictionlessly. And no matter where you are in your transformation journey, humility never backfires. One common trait in high-performing teams? They learn from failure and quickly adapt to find workarounds. Myler believes there are two Hs to cruising through this supply chain journey: “The first H stands for a hypothesis. We have a strong hypothesis of where we're going, which speaks to the vision. And the second H is humility. Don't assume you know all the answers going in. And I've stuck with that. It actually works."
Humility and curiosity train great leaders. The supply chain ecosystem needs ownership-based roles in which people can be fearless to break transformation barriers.
Supply chain metamorphosis is a slow process
But worth the effort. When evaluating supply chain challenges and transformation initiatives, keeping two principles and one core truth in mind is invaluable. In our experience, the first principle – transformation – requires both investment and commitment to plan, execute, and above all, course-correct hypotheses, models, and technological assets.
The second principle – companies require new operating models to manage the volatility of today and ensure agility for tomorrow. But above all, the core truth must not be lost – even with technological advancements, people are still at the heart of both innovation and transformation. Talent re-skilling, developing a shared vision with data-driven hypotheses, and investing in personal relationships are often underinvested areas that hold the keys to adoption and value creation.
A lot is riding on the teams that work day and night to meet changing preferences and keep pace with delivery needs. Businesses were always under pressure. But today, conditions are different. Our teams require better visibility into their operations through the democratization of data and analytics. Are we there yet? No. But organizations need to act today for a future full of possibilities. This begins with people. And how fast you can empower your teams to attain digital transformation that is real and data driven.