- Point of view
CMC operations: Selecting the right operating model
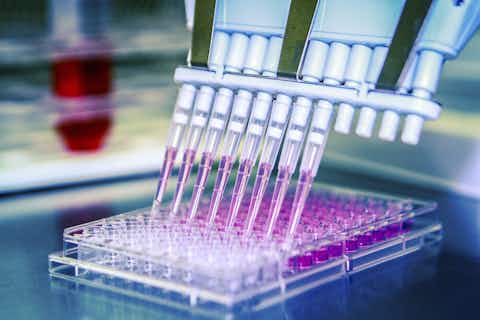
Life Sciences companies are facing increasingly stringent regulatory requirements in developed markets and the challenge of satisfying dramatically varying requirements in emerging markets, which result in penalties for non-compliance and costly delays. Regulatory affairs outsourcing, especially for chemistry, manufacturing, and controls (CMC), can address some of these challenges by increasing throughput and efficiency in CMC operations. However, selecting the right operating model requires a thorough understanding of the options available. This paper profiles operating models to help regulatory affairs leaders choose the most suitable target operating model.
The Life Sciences industry has faced unprecedented regulatory scrutiny over the last few years. In research[1] commissioned by Genpact, 72% of senior executives across the Life Sciences sector cited ensuring compliance with regulations as one of the three most important challenges in their company. Health authorities around the world are subjecting pharma products and processes to stringent reviews. As a result, compliance departments are overwhelmed with multiple responsibilities that must be routinely performed to unforgiving levels of accuracy—which stifles capacity and increases operating costs and response times. The continued push in emerging markets is also increasing compliance risks, and the need for faster time-to-market adds to operational complexity.
Regulatory affairs CMC operations struggle with complex and rapidly growing responsibilities
Regulatory affairs assume a significant share of these complex CMC operations. CMC regulatory professionals are responsible not only for CMC-related documentation for review by health authorities around the world, but also documentation that addresses the frequent changes in drug substance and drug product manufacturing sites. CMC regulatory professionals also provide annual reports and renewals to ensure continued market access for a pharma company's product portfolio. These professionals also help the manufacturing sites remain “in compliance." In addition, the increasing requirements of health authorities around the world for greater detail on the CMC section of pharmaceutical marketing applications is putting more demands on industry and CMC operations regulatory professionals.
New operating models help regulatory professionals focus on the enterprise's priorities
Leaders in the industry are responding to these challenges by revisiting the operating model so the highly educated and highly skilled CMC regulatory professionals focus on the company's highest priorities. Advanced operating models such as outsourcing standardize and consolidate routine lower-value tasks to deliver predictably and at scale by leveraging external resources. Outsourcing is a practical CMC regulatory solution that makes prudent financial sense in the “belt-tightening" environment in the pharmaceutical industry.
Numerous models are currently applied to CMC regulatory affairs outsourcing. These models usually evolve over time as the client–consulting firm relationships matures and increasing levels of trust are built (see Figure 1). The first group of models includes the isolated individual assignments, outsourced employee clone, and close project partnership. These models have been used for years in the consulting industry, but over time, the impact due to the maturing client–consultant relationship plateaus. Functional and portfolio outsourcing, usually applicable to more mature functions and products, is the next stage in this evolution that has the potential to generate still more impact.
The following is a brief description of the primary options.
Isolated individual assignments
This is the original outsourcing CMC regulatory consulting model in which one-off individual tasks, most often determined by the product or project owner, are delegated to a CMC regulatory consultant. This model is quick to implement, but consultants may need to be trained on client systems and processes, which adds 20 to 30+ days of lead time before the consultants can start contributing. In addition, if there are gaps between projects, the consultant may need refresher trainings on new SOPs or standards.
Often used to add capacity during peak workload periods, this model is neither efficient nor sustainable, since the consultant will likely need to learn about the project background and client processes each time.
This is usually the pilot model for new client–consultant relationships.
Close project partnership
In this model, the CMC regulatory consultant works closely with the client as a second pair of expert hands supporting one or more high-profile or high-priority projects during peak periods. The primary advantage of this CMC regulatory consulting model is that the consultant comes up to speed on the project(s) much faster due to the close client partnership. There is often synergy in this pairing, due to the consultant's cross-company experience and best practices, which are shared with the client. In this model, the high-profile products or projects get the immediate attention they deserve, but often with no significant efficiency gains if the consultant also needs to be trained on client-specific systems and processes.
This model usually works best with highly experienced client staff and highly experienced consultants. It is used to a lesser extent due to the cost of a “premium" consultant.
Outsourced employee clone
This model is usually utilized to augment client staff. The CMC regulatory consultant functions in the same role as a client employee, with similar project and product assignments. Such CMC regulatory consulting support is typically provided for established products since clients usually assign newer projects to highly experienced employees.
In this model, capacity can be added without the fixed costs of adding employees (increased benefit costs, indeterminate pension costs, etc.). The consultant's product and system knowledge increases quickly, so less client hand-holding is necessary.
This model normally requires highly skilled consultants, as the consultant must be familiar with various tasks to be of value to the client. The consultant may still need to be trained on client systems and processes, which adds 20 to 30 days before he or she is a functioning contributor.
Functional outsourcing
Using this model, the consulting firm takes on an entire function or role for the client company.
Since the consulting firm specializes in one or more tasks, efficiency is gained through the use of a streamlined, focused process, which reduces the overall cost to the client. Higher levels of efficiency can be achieved through consolidating functions across business divisions and geographies and applying process optimization techniques such as Lean Six Sigma to tasks that are transactional and voluminous, for example, variations. A recent example illustrates the efficiency gained when the preparation of CMC renewal packages was outsourced:
When using such a model, only the subset of client-required trainings relevant to the functions is necessary. Consolidating and streamlining a function for outsourcing often allows the operations to be performed at off-shore locations. Minimal client supervision is required since the consulting firm has end-to-end accountability for the outsourced function. As a positive for the client and the consulting firm, this type of work closely matches the skill and experience of CMC regulatory consultants with the expertise required for specific functions.
This CMC regulatory consulting model works extremely well in practice, allowing the client to focus on what is most important to their business and the consultancy to concentrate on tasks they can do more efficiently than the client.
Portfolio outsourcing
In this model, the entire portfolio (usually of older, established products) is outsourced. The consulting firm assumes responsibility for all the functions necessary to support the portfolio; thus, the client's staff can focus on new projects or products to support the future growth of the organization.
A disadvantage of this model is that CMC regulatory consultants will likely use the client's systems for much of the end-to-end process; thus, the consultants must complete training on the client's systems and processes.
The choice of the right consultant partner is critical as smaller organizations may experience employee churn, due to the narrow focus and lack of growth opportunities. However, CMC regulatory consulting organizations with a global footprint and a broad array of services can attract and retain talent by offering education and growth opportunities across multiple clients.
Path to a viable operating model
CMC regulatory affairs functions are gradually transitioning to more advanced outsourcing models as early adopters of models 4 and 5 (isolation of a function or role, portfolio outsourcing) are already reaping the benefits of these more efficient and cost-effective models. Hybrid models combining one or more of these models have also been used to support the regulatory CMC operations function. For example, the preparation of the CMC sections of all renewals and annual reports may be completely outsourced, but the close project partnership model might be needed to support high-priority, high-visibility NCE submissions.
Significant experience is necessary to navigate this continuum of operating model choices, and CMC regulatory affairs have certain unique requirements and challenges that have material implications for choices in outsourcing relationships, resourcing, and delivery models.
Many post-approval CMC changes are driven by the client's major manufacturing sites. Consultant staff placed at the actual manufacturing site can build better relationships with the staff and shorten lead times. The hands-on visualization of the manufacturing process often leads to better understanding of post-approval changes and increases the ability to completely and efficiently author process change descriptions and documentation. Consulting firms can struggle with placing consultants at manufacturing sites since firms may not have staff who speak the local language and are near plant sites.
However, global service delivery capability is useful not just for favorable cost structures but also for the ability to provide around-the-clock support. For example, this can be extremely helpful immediately before an NCE submission. Such support can also be helpful when supporting hospital and government tenders, as a rapid response may be crucial in winning the contract.
While selecting the appropriate outsourcing models, a pragmatic view of the assignments and their relative priority is critical. Ideally, a portfolio of project types of various durations (short- and long-term projects) and various priorities that can be distributed to balance workloads will maximize utilizations and efficiency. If most projects are high priority and have short lead times, then capacity requirements and efficiency can be affected.
The time and effort needed to respond to health authorities' inquiries are escalating, and designing the operating procedures for “first-time-right" deliverables is critical to ensure timely responses. Implementing an internal quality assurance review and a second regulatory review is no longer a “nice-to-have."
CMC regulatory professionals rely on electronic regulatory systems for control change management, document authoring, and publishing. These systems and processes can be cumbersome and challenging for new employees to navigate. However, when large firms have been acquired or merged with other large firms and the systems are patched to fit the new processes of the blended organization, problems arise. As a result, CMC regulatory professionals end up spending expensive time navigating the electronic systems rather than focusing on the regulatory sciences aspect of their work.
A regulatory system subject matter expert (System SME) responsible for thoroughly understanding the regulatory systems and staying up to date with system updates or changes, as well as progressing the regulatory consultant's submission through the electronic systems, can help bridge this gap. Assigning the right person to the right role allows highly skilled CMC regulatory consultants to focus on regulatory sciences and regulatory System SMEs to focus on navigating the ever-changing electronic regulatory systems, maximizing efficiency for both roles.
Conclusion
We are on the cusp of the explosive transformation of operating models in the world of regulatory affairs—especially through outsourcing in the CMC operations area. In spite of changes implemented by the major markets through the International Conference on Harmonization, the regulatory environment continues to become more complex in emerging markets, and requires more regulatory effort than ever before. This is true not only on the pre-approval side but also on the post-approval side of the equation, where the submitted number of CMC-related changes is increasing each year. The growth of regulatory departments within individual companies cannot be sustained. Outsourcing with the appropriate model or models can add increased throughput with increased efficiency. CMC regulatory affairs leaders can accelerate the path to value by leveraging the experience curve of similar organizations and combining it with a clear understanding of the options, strategic needs, and current capabilities.
View our life sciences page
Independent research commissioned by Genpact to assess the potential for new operating models across a wide spectrum of industry sectors and functions. More than 900 senior-level executives screened based on their ability to materially influence functional decisions completed the survey. These findings were drawn from the responses of 120 senior Life Sciences R&D executives.