- Point of view
Consumer goods and retail supply chains in 2025: Meet the supply brain
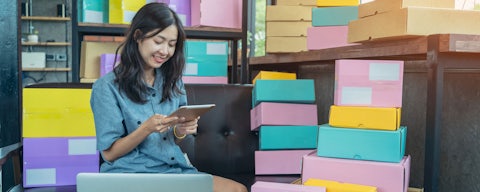
Over the next decade, consumer packaged goods (CPG) and retail businesses will turn to supply chains to solve key industry challenges. The desire for convenience and personalization, awareness of the environmental impact of consumption, and fears about trade disruptions and fluctuations in cost are all challenges that can be solved with more connected, agile, sustainable supply chains. With all eyes on this part of the business, there is a huge opportunity for supply chain leaders to drive change: implementing the latest digital technologies to build the required agility for new consumption models. According to Genpact's Consumer Packaged Goods and Retail in the Age of Instinct report, with this in place, the supply chain will function more like a supply brain.
As Mike Landry, supply chain service line leader at Genpact, explains: "The companies that succeed in the future will run supply chains as one ecosystem, using data, digital technologies, and artificial intelligence (AI) alongside human intelligence to work as one supply brain connecting multiple links that all have to work in sync."
Here we look at three attributes of the supply brain, and how they will enable CPG and retail companies to succeed in 2025.
Tuned to individual customer needs
Laser-focused demand-sensing technology will combine statistical forecasting algorithms, AI, and internet of things (IoT) devices to make more accurate predictions of demand than current models that rely on historical data. This technology will enable businesses to anticipate and prepare for individual customer purchases, in some cases before the customer is even aware of a need for them. Running out of household essentials and groceries will become a thing of the past.
With permission from the consumer, organizations will be able to convert data from smart homes, browsing history, and in-store behavior into supply chain responses: reordering when stocks get low; making proactive purchasing suggestions when the time is right; and even restocking shelves in the customer's office or home.
Both Walmart and Swedish supermarket group ICA have recently announced plans to deliver groceries directly to their customers' cupboards and fridges, strengthening the relationship between the brand and the consumer. In the future, food and drink products could be automatically ordered and delivered, triggered by the consumer removing an item from their shelf and sensors sending that signal back to the supply brain.
Retailers will also tap into personal data to elevate the customer experience. Microsoft and Kroger are piloting connected experience stores focused on driving personalization. Smart shelves in stores indicate price, promotions, and nutritional data. Customers use an app to create a shopping list in advance, which synchronizes with the in-store smart shelves to guide and inspire them as they move through the store. The result is a personalized experience for each customer that deepens connections with manufacturers and retailers.
Consumer packaged goods and retail in the age of instinct
Integrated real-time insights
The key to the supply brain sensing and reacting to personalized consumer data will be its data-processing capabilities. Whereas data and decision-making are now often restricted to distinct silos within the business, the supply brain relies on integrated operations, so marketing, sales, procurement, and logistics all work from one set of data across the supply chain. Armed with an iPad and dashboard interface, decisions will be based on accurate forecasts and up-to-date performance metrics. With this level of visibility, sales teams will be able to assess the true profitability of a trade promotion.
For example, as Genpact's consumer goods and retail supply chain lead Nikolas Coffrin explains, one client he works with is currently implementing technology to make quick decisions based on targets. "Business performance should dictate your decisions," he explains. "We're working with a large beverage manufacturer that can review performance against the yearly plan and targets every month so it can update its strategy on a monthly basis. It can pull back on planned promotions if the data shows the business is hitting revenue targets but not hitting margins."
In order for businesses to meet consumer expectations to shop anytime and anywhere, consolidating data across all the links in the supply chain also needs to include order management systems. Integrated operations offer better visibility of inventory and quicker deliveries to customers. No more lost revenue from missed delivery targets or empty shelves.
Local and agile
The disruption to global supply chains by the COVID-19 pandemic has brought the need for greater resilience into sharp focus. Reliance on far-flung suppliers and restrictions on movement across the world meant production and movement of goods slowed to a crawl. The desire to ensure continuity of supply will accelerate the trend of shrinking and localizing supply chains to minimize the impact on the environment.
Alibaba's supermarket chain Hema is a pioneering example, with each location acting as a warehouse, store, and online fulfillment service for the local customer base within a 3-kilometer radius of the store. The store relies on data analytics to determine the stock it should sell and ensure all orders are picked and delivered in just 30 minutes.
Taking inspiration from smaller CPG companies, global conglomerates are increasingly working with contract manufacturers to control instead of own production. This will enable supply chains to expand and contract with demand and speed up innovation with quicker product launches.
We've seen early signs of the supply brain in action as CPG and retail firms adjusted supply chain strategies during the recent disruption. One manufacturer quickly automated order capture processes to cope with a surge in demand, while another automated critical parts monitoring to ensure continuity of supply to its customers.
Investing in a supply brain that can respond with agility during a crisis not only keeps the business running in the short term, but also builds investor confidence and long-term value.
The result? Closer to the customer
Adapting to increased consumer expectations for convenience, sustainability, and cost savings adds to the complexity of the supply chain. This is both a challenge and an opportunity. The advantages of this more intimate supply chain are substantial because it encourages a closer relationship between manufacturer, retailer, and customer. This deeper level of engagement, which most brands long for, will come down to how well organizations preempt the shift from running supply chains to orchestrating supply brains. The winners will use AI as their neural wiring, collaborate with all partners across the supply chain, share data across connected ecosystems, act on predictive insights, and empower adaptive workforces.