- Case study
Making plastic fantastic
How process visibility cut the carbon footprint and boosted quality for a plastics manufacturer
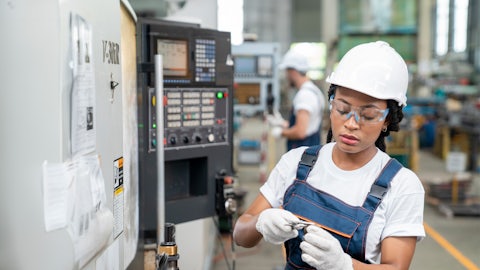
Who we worked with
A major player in the chemical industry, excelling in high-end plastics, petrochemicals, agri-nutrients, and metal products with a deep commitment to clean energy.
What the company needed
The company wanted to improve end-to-end process visibility, ramp up manufacturing, assure quality, and introduce steps to accelerate carbon neutrality.
How we helped
- Designed and implemented a system to capture real-time plant process data
- Introduced lean production practices
- Reduced the IT footprint
What the company got
- Real-time visibility of manufacturing processes with the ability to track nearly 100,000 process values
- Smart manufacturing capabilities with real-time feedback from machinery for predictive maintenance
- IT savings of $100,000 annually through the use of open-source software and lean initiatives
- $1.7 million in savings with 42% fewer support requests
- An average of $1 million per annum saved on quality spend
- Order fulfillment improved by six days, elevating supply chain performance
- A 10% quality improvement through better production management and root cause correction analysis
- A 60% boost to on-time deliveries
The challenge
A better way to monitor machines
With a 20-year partnership under our belt, when our client pledged to go carbon neutral by 2050, we saw a valuable opportunity to use our operational knowledge to help achieve this vision.
The company's extensive use of diverse industrial automation equipment across 60 global factories for high-end plastics production contributed to its carbon footprint. Without regular maintenance of machines, operational efficiency took a hit. Plus, it led to an increase in energy consumption and emissions. The result? A less-than-perfect product quality.
The client wanted to redesign monitoring equipment maintenance, minimize machine downtime, and quickly test products on the factory floor to maintain product quality. But this was a complex task. To ensure good quality, the machines in the production environment needed 5,000–6,000 predefined operational parameters. These machines generated 100,000 data points every few seconds – data that could help monitor the production process better and support engineers in maintaining quality benchmarks, getting better process visibility, and proactively supporting incidents (or issues). Instead, its team got pulled into fixing incidents rather than understanding these data points and focusing on quality.
The solution
End-to-end process visibility
We ran a complete assessment of the client's factory operations. What surfaced was a lack of a strong automation strategy in its production processes. This automation gap and irregular maintenance schedules prevented the company from reaching production capacity. So, we worked closely with process automation engineers, production managers, and IT experts to provide an effective solution.
Our solution had three key elements:
- We worked with the company to build intelligent processes by gathering real-time insights on machine operating frequency. We secured and integrated its operational technology and information technology (OT/IT) stack and deployed process modeling to accurately predict a machine's current state and future state.
- We introduced lean scheduling by analyzing past order patterns and estimating machine usage – an optimal way to automate and maximize production levels.
- To reduce support incidents, our team rolled out fortnightly knowledge transfer sessions to help the client's team correctly route maintenance requests.
Impact
A leap towards leaner processes, smarter factories, and carbon neutrality
We implemented our smart manufacturing and lean scheduling solutions at all 60 manufacturing sites. With real-time visibility of plant operations and decision support, process engineers can now quickly address problems while maintaining production levels and quality at a reduced cost. Our solution delivered a list of impressive outcomes:
- $1.7 million saved as a result of 42% fewer support requests
- An average of $1 million saved per year on quality costs with real-time monitoring
- Order fulfillment improved by six days
- 60% more on-time deliveries with 10% better product quality
- $100,000 saved annually by switching to open-source software instead of paying for costly licenses
Along with these headline impacts, we helped the client predict upcoming maintenance to cut operational costs – supporting its carbon neutrality goals by improving energy efficiency and easing the environmental strain.