- Solution overview
Manufacturing supply chains: supply chain design
Balance manufacturing, inventory, and transportation demands to stay ahead of the competition
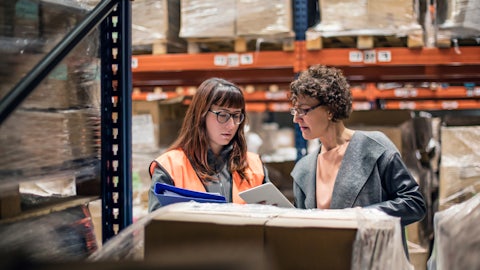
The challenge: tame supply chain complexity while managing costs
Manufacturers' customers are becoming more demanding every day. They want the perfect order: accurate paperwork delivered electronically, a 100% order fill rate, and on-time delivery. And if that isn't enough, they need it at the lowest possible cost.
It takes a finely tuned supply chain to meet these expectations. Companies must manage complex variables including procurement, manufacturing, inventory, fulfillment, and transportation. Add in trade-offs between capital investments, operating expenses, cycle times, and capacity, and the scale of the challenge is clear.
But successful manufacturers must rise to this challenge. They must exceed customer expectations with a slick supply chain network that coordinates demand planning, inventory control, supplier inventory management, and logistics.
Take a copy for yourself
What we offer: granular research, solid design, detailed strategy, and a clear roadmap
Creating this ideal supply chain calls for a deep dive into each client's individual needs.
We start with a current-state assessment to get a baseline of supply chain performance. This baseline simulates historical performance and assesses the many variables that affect operations, such as inventory, network, transportation, and cost-to-serve.
We work with clients to understand their supply chain operating goals, analyzing the research findings to develop future-state strategies that will achieve these objectives. We do this by evaluating each of the desired changes with a highly structured, iterative approach using Llamasoft Supply Chain Guru. This builds scenarios such as predicting how minimizing transportation costs or reducing the manufacturing footprint will affect performance. Then we undertake qualitative and quantitative financial and risk reviews of the top three scenarios before finally recommending the design that best meets business goals.
Finally, once we've agreed the design, we outline the transition tasks and one-off costs and make recommendations for sequencing and cash flow. Figure 1 outlines all the phases involved.
Figure 1: Genpact's approach to supply chain design
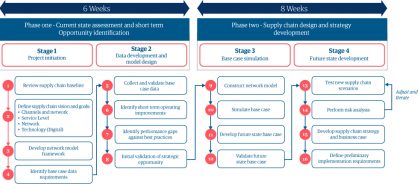
The result: a transparent and coordinated supply chain for informed decision-making
We create truly holistic solutions to customers' supply chain challenges. Our clients receive a three-to-five year design, the business case to support it, and a roadmap to get them there with clear-cut customer service and performance goals. Our output includes:
- A supply chain strategy that defines plant-to-distribution center assignments
- A thorough assessment of the location, form, and function of distribution centers, transportation lanes, and throughput
- Assessing opportunities to reduce cycle times across the supply chain
- Re-engineering of third-party logistics
- A cost/benefit analysis covering implementation and projected savings
Case study
Designing the supply chain of the future for a fast-moving consumer goods company
This global manufacturer was missing supply chain targets because of outdated, fragmented IT infrastructure and inconsistent data. Introducing new products into the supply chain required improved planning capabilities and closer collaboration with suppliers.
We started by assessing the current supply chain's functional and technological landscape, identifying the levers it could use to improve processes and systems. Armed with this information, we then put forward a proposal for an integrated and holistic supply chain design that improved its resource requirement planning capabilities. The client received:
- A supply chain excellence roadmap with concrete next steps for strategy, processes, organization, data, and systems
- The business case for a scenario planning tool
- Awareness on process and tool gaps
- Recommendations on how to improve resource requirement planning along the supply chain, including late customization, upstream flexibility upstream, and responsibilities